The Green Houses Roedean, Brighton
6 January 2022
Overview
Basement type: Refurbishment |
Building type: Residential |
Type of waterproofing: Type C |
Member: Delta Membrane Systems
|
Delta Registered Installers, Bensley’s were appointed by main contractor, Minton Young on behalf of BAOBAB Architects to provide a maintainable waterproofing solution to a large prestigious development in the Roedean area of Brighton, overlooking Brighton marina.
The scope of the works was to design, specify and install a suitable waterproofing solution to 2 large properties engineered from ICF construction which required waterproofing. Areas where attention from a skilled specialist were required, was to the rear and two side walls which were earth/ground retaining.
When specifying a suitable waterproofing solution, consideration to the final use of the building, designing a system to be maintainable and repairable along with a deep understanding of BS 8102:2009 is essential in ensuring project success.
From a waterproofing design perspective, we use three grades to define waterproofing systems.
These 3 grades are:
- Grade 1 – Some water seepage and damp are tolerable depending on the intended use
- Grade 2 – No water penetration is acceptable
- Grade 3 – No dampness or water penetration is acceptable
In existing basements and new build properties which will be habitable, Grade 3, is always required.
Methodology
Although a relatively new concept in the UK, ICF homes are extremely energy efficient. ICF homes (Insulated Concrete Formwork) comprise of large polystyrene blocks that are lock together to form a house shape into which concrete is poured to form the wall structure. Prior to Bensley’s being appointed the concrete floor slab had already been laid, Bensley’s suggested applying as a closed layer, Koster NB 1. NB1 is waterproof to pressurized water up to 13, bar and develops an intense bond to the substrate and plugs capillaries following an anti-lime inhibitor.
Free lime can leach from newly poured concrete and can lead to the formation of calcium carbonate or calcium sulphate on the surface, using an anti-lime inhibitor to concrete surfaces prior to the installation of a cavity drainage system prevents leaching.
Once the ICF walls were constructed, Bensley’s applied Koster Deuxan 2C to the exterior. This robust crack-bridging 2 component polymer modified bitumen is designed as a secure and permanent exterior waterproofer, which included a flexible fillet at the floor/wall junction. This was then protected by the ground workers prior to back filling incorporating a suitable land drain to the perimeter.
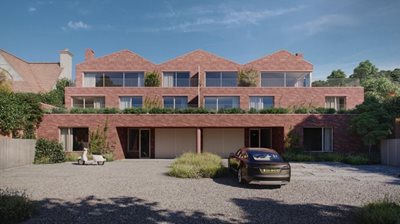
Internally, Bensley’s proposed to future proof the project by installing Delta’s MS 500 Fire Retardant, Type C Cavity Drain Membrane System, which was installed with Delta plugs, tape, and Delta fire retardant overtape.
In principle a Cavity Drainage System allows for moisture or running water to travel behind the membrane in a controlled drainage system. Whilst requiring minimal preparation and disturbance to an existing substrate.
Below the floor membrane (Delta MS 20) perimeter drainage channels with flushing outlets were sited within rebates allowing for suitable drainage of any future water ingress and being diverted to suitable discharge points. This incorporated a suitable closed cell floor insulation.
Due to the sloping side, any ingress of ground water was to be discharged to the front elevation where the drainage system was converted to suitable pipework and non-return values to a soak away to the front of the building by gravity fed drainage, all of which was tested prior to the main contractor continuing with the floor screed and following build up construction as required.
Products:
Koster Polysil TG 500
Koster NB 1 Grey
Koster Deuxan 2C
MS 500 Fire Retandant Type C Membrane
MS 20
Delta Channel
Results
The client was delighted with Bensley’s pragmatic and practical approach to this project, assured that these luxury properties will be preserved for years to come, given Delta’s 100-year product life cycle.
By keeping a proactive approach, the design and layout of a building, in conjunction with the materials used and style of construction, play a key role in preventing the spread of fire and will allow the safe evacuation of occupants from a building in the event of a fire.