1-9 Seymour Street, London
15 May 2017
Overview
Basement type: New build |
Building type: Mixed use |
Type of waterproofing: Type A & C |
Member: Delta Membrane Systems |
Other: Constrained site |
|
The Project
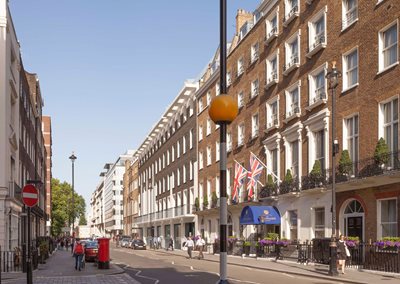
In 2015, Westminster City Council's planning department granted The Portman Estate planning permission to demolish the existing building at 1-9 Seymour Street and to redevelop the site. The scheduled demolition and clearing of the site was to make way for a new seven storey mixed use building, which was to include a two level basement, residential block, restaurant, retail space, commercial office block and school.
Some of the key challenges to this project were:
- Ensuring a fully functional waterproofed basement which would accommodate the building and its future use.
- Responsibility for full façade package including onerous performance criteria.
- Multiple façade treatments with complex interfacing including totally bespoke projecting glass and steel bays.
- Bespoke vitreous enamel window liners.
- Complex inner city environment with significant delivery challenges.
Methodology
1-9 Seymour Street was a 90,000ft2 technically challenging project with a multiple façade types. Both Delta Membrane Systems Ltd and Guardian Preservation were included at the design phase so were able to give expert advice during the crucial planning stage. The basement dig was planned with the use of piling. On this project contiguous piling was deployed in
conjunction with an inner RC lining wall.
Tim Herbert, CSSW qualified Structural Surveyor and partner at Guardian Preservation commenced his involvement in the project by giving careful consideration to products available, how they would be best suited to the project, that all BS8102:2009 standards and considerations were met, that the site was kept in a safe manner (health and safety) and that all Building Regulations were adhered to.
Tim’s approach to the project was to initially make contact with Delta Membrane System Limited’s David J Symes, Technical Director. As with any basement construction, consideration to groundwater, soil type, precipitation, topography and ground conditions/site analysis needed to be addressed.
System Components
With over 2500m2 to cover it was decided that Delta Membrane Systems Limited’s NB1 in-depth migratory crystalline slurry (a Type A System, a water barrier), and Delta MS500 and Delta MS20 (a Type C System, cavity drain membrane system) would be incorporated. An initial and important consideration in the overall waterproofing strategy was to ensure that all construction joints were appropriately detailed and waterproofed using Hydrophylic waterstops – such as Koster Quellband, which expands in contact with water to seal the construction joint.
Köster NB1 is a crystallizing mineral waterproofing slurry system which has a capillary plugging agent ideal for sealing against pressurized water (> 13 bar) and is watertight (>130m water head). Tim opted to apply the Köster NB1 with a peristaltic pump providing a uniform spraying application, this method saves considerable man hours and is a great way to ensure complete even coverage.
Having applied a Type A waterproofing system Tim opted to add a secondary Type C system offering a robust waterproofing design.
By adding a secondary Type C system the basement would be completely watertight, if any water ingress was to occur in future the Type C system would be able to deal with this so as not to compromise the structure. The Delta NB1 KosterMS500 is a premier cavity drain membrane and was used for the waterproofing of the walls. The Delta MS500 was fixed using Delta Qwik-seal plugs, at 600mm centres with added benefits of Delta double-sided butyl tape to seal joints and overlaps. Delta butyl Corner strip tape was added to seal wall/floor joints.
The Delta MS20 is a champion cavity drain membrane used of waterproofing the floors. This is a heavy gauge version and incorporates 20 mm studs which offer extra drainage capacity. Delta MS20 was used as a “cavity former” for this type of new construction. The Delta MS20 is neatly rolled out across the basement floor; the sheets are overlapped and sealed in accordance with the manufacturer’s instructions. Corner strip tape was added to seal wall/floor joints.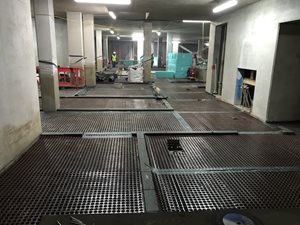
Results
The basement structure has been constructed to cope with any future water ingress and will withstand the test of time.
Galliford Try were thrilled with the outcome and the project was achieved on time and within budget.
The finished project a truly stunning building that adds to the growing portfolio for all involved and will add to London’s ever evolving skyline and landscape.
See Delta Membrane Systems' Company profile here